Expert Framing Services in North Bay
MHM General ContractingPrecision Framing for Residential & Commercial Projects
A strong, well-built frame is the foundation of any successful construction project. At MHM General Contracting, we specialize in professional framing services for residential homes, commercial buildings, and outdoor structures in North Bay, Ontario. Our expert house framing team ensures precision, durability, and compliance with Ontario’s building codes to create structures that last.
Whether you need wall framing, roof framing, deck framing, or full-scale timber frame construction, we handle projects of all sizes—from custom homes to large commercial buildings.
Searching for “Expert Residential Framing Contractors Near Me”? Get Your Free Quote Today!
Experienced Craftsmen – Skilled in wood & steel framing techniques.
Framing Inspection and Code Compliance – Hassle-free approvals.
Exclusive Savings – Save 5% with our Preferred Membership!
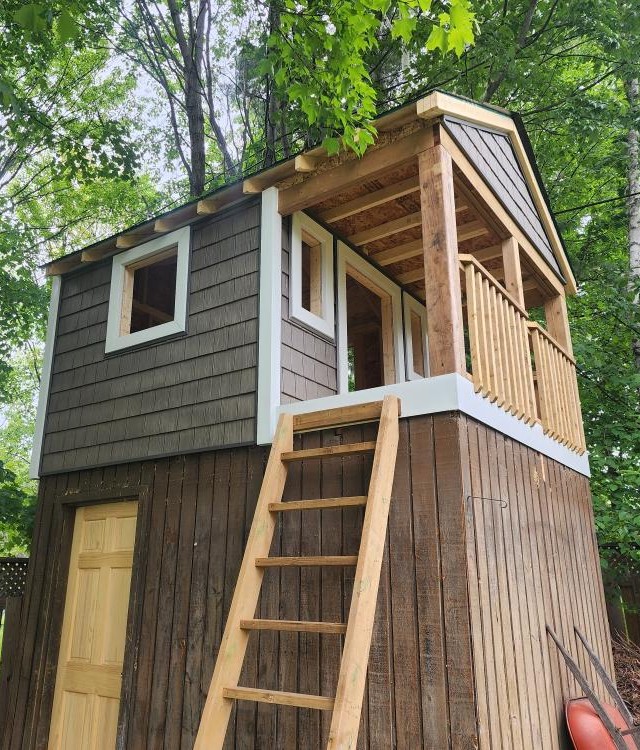
The Best Choice
Why Choose MHM General Contracting for Your Framing Project?
Local Expertise
We understand North Bay’s climate, soil conditions, and building regulations.
Commercial Building Framing Specialists
Skilled in wood & steel framing for businesses and industrial buildings.
Framing Estimates and Project Planning
Detailed cost breakdowns & scheduling for a stress-free build.
Code Compliance & Inspections
Ensuring your framing meets all safety and structural standards.
From new builds to home additions and large-scale commercial projects, our framing solutions provide the strength and precision your project needs!
Expert SolutionsOur Comprehensive Framing Services in North Bay
Residential Framing
- House Framing – Structurally sound homes with expert wood or steel framing.
- Wall Framing – Strong, load-bearing walls designed for long-term stability.
- Roof Framing – From simple gable roofs to multi-pitch structures, built to withstand Ontario weather.
- Deck Framing – Sturdy, weather-resistant decks for outdoor living spaces.
Commercial Framing
- Steel Framing & Wood Framing – Custom solutions for offices, warehouses, and retail spaces.
- Large-Scale Framing Projects – Multi-family properties, industrial sites, and business expansions.
- Framing Inspection and Code Compliance – Meeting all Ontario building regulations for hassle-free approvals.
Quality Timber Frame Construction
- Traditional & Modern Timber Framing – Handcrafted joinery blended with engineering precision.
- Eco-Friendly Materials – Sustainably sourced timber for durability & aesthetics.
- Custom Designs – Open-concept frames, exposed beams, and unique layouts.
No matter the size or complexity of your project, our team ensures expert framing solutions from start to finish!
Pros and ConsSteel Frame vs. Wood Frame
Choosing the right material for your framing project depends on cost, durability, and intended use.
Feature | Wood Frame | Composite Frame |
---|---|---|
Durability | Strong, long-lasting | Fire & pest resistant |
Cost | More affordable | Higher upfront cost |
Flexibility | Easier for renovations | Ideal for large commercial builds |
Eco-Friendly | Sustainably sourced options | Recyclable material |
Not sure which material is best for your project? Our team will help you choose the right framing solution!
step-by-stepThe Framing Process:From Blueprint to Build
We follow a proven step-by-step process to ensure precision, durability, and efficiency in every framing project.
1
Step 1: Free Consultation & Framing Estimates
- Discuss your project goals, budget, and timeline.
- On-site evaluation to assess conditions and provide cost estimates.
2
Step 2: Custom Framing Design
- Tailored plans for maximum structural integrity.
- Expert recommendations for steel frame vs. wood frame construction.
3
Step 3: Material Selection & Preparation
- Choosing high-quality wood or steel for your framing project.
- Prepping the site for efficient, organized construction.
4
Step 4: Precision Framing Construction
- Expert wall framing, roof framing, and deck framing.
- Laser-guided leveling and advanced tools for perfect alignment.
5
Step 5: Framing Inspection and Code Compliance
- Rigorous quality control checks throughout the process.
- Final inspection to ensure code compliance and structural integrity.
From custom homes to commercial buildings, we deliver framing solutions that last a lifetime!
High-Quality
Specialized Framing Services
Deck Framing
- Sturdy foundations for decks of all sizes.
- Designed for long-lasting outdoor use.
Roof Framing
- Gable, hip, and multi-pitch roof structures.
- Built for weather resistance and durability.
Timber Frame Construction
- Classic craftsmanship meets modern engineering.
- Stunning open-concept wood framing designs.
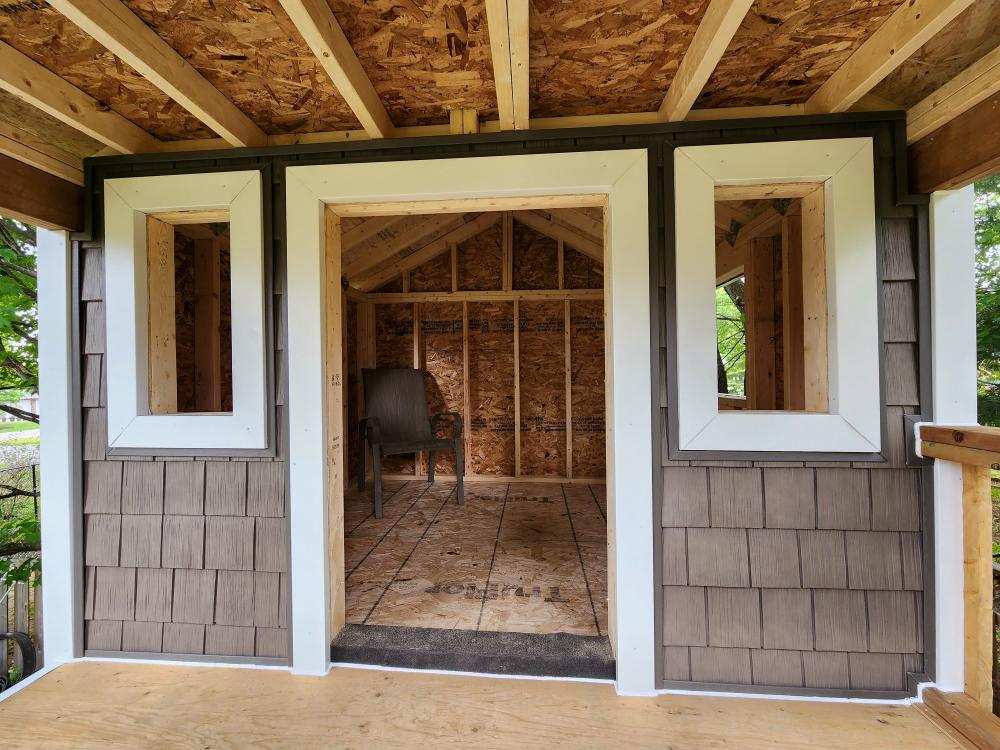
Delivering PrecisionOur Framing Projects
From residential homes to large-scale commercial buildings, we take pride in delivering precision framing that lasts.
Call now to schedule your free consultation!
What Our Clients Say – About Our Framing Services
Join the many homeowners & businesses who trust us for high-quality framing solutions!
Build Your Dream
Ready to Start Your Framing Project?
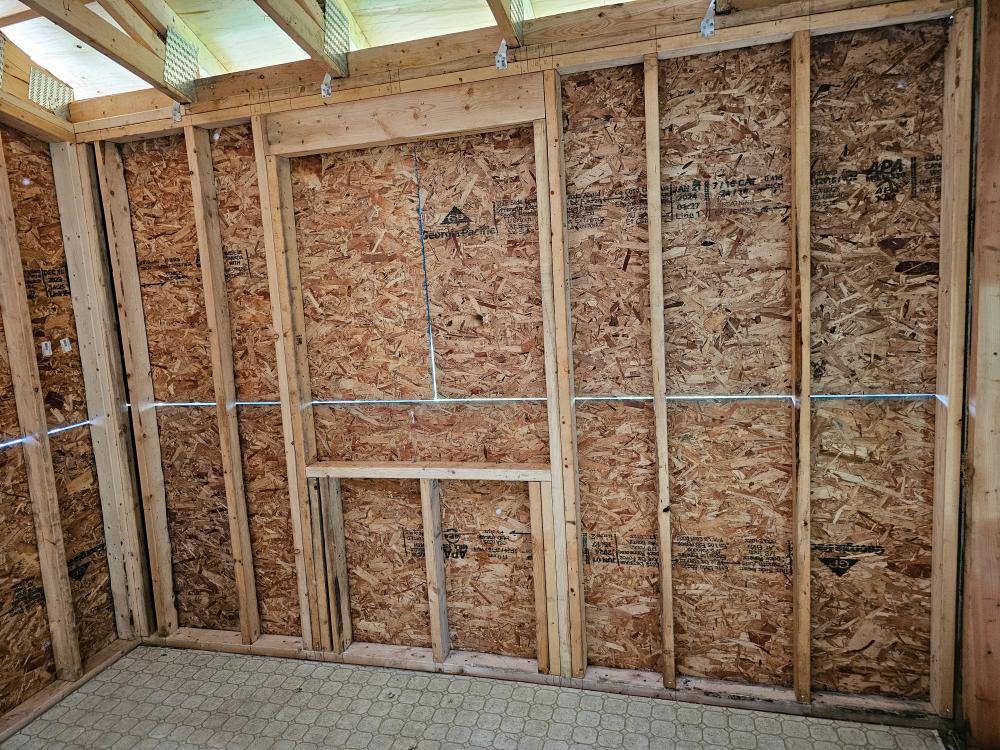
Get Your Free Framing Quote Today!
At MHM General Contracting, we specialize in expert framing services that provide the structural integrity your project needs. Whether you’re building a new home, adding an extension, or framing a commercial building, we’re here to help.
Call us:
(705) 303-3340
Visit us:
245 Mattawa Street Unit B, North Bay
Exclusive Offer:
Save 5% on your framing project!
Ask about our Maintenance Membership Program for additional savings!
FAQsYour Framing Questions, Answered
What is the difference between load-bearing and non-load-bearing walls?
Load-bearing walls support the weight of the structure above them, while non-load-bearing walls (also called partition walls) only support themselves. Here are the key differences:
Load-bearing walls:
- Transfer weight from the roof, upper floors, and other structural elements to the foundation
- Are typically exterior walls, but can also be interior walls in larger structures
- Removal or modification requires careful engineering and temporary support structures
- Often contain larger studs (2×6 instead of 2×4) spaced closer together
- Usually run perpendicular to floor joists or roof trusses above
Non-load-bearing walls:
- Primarily serve to divide interior spaces
- Can be removed or modified more easily without affecting structural integrity
- Typically use 2×4 studs spaced further apart
- Often run parallel to floor joists or roof trusses above
When planning renovations or modifications, it’s crucial to identify which walls are load-bearing. This usually requires consulting building plans or hiring a structural engineer to assess the home’s framing.
2. How do I properly frame a window or door opening?
Framing a window or door opening requires careful planning and execution to ensure structural integrity and proper fit. Here’s a general guide:
- Determine rough opening size: Add 1 ½ – 2” inches to the window or door’s actual dimensions.
- Cut the rough opening:
- For load-bearing walls, install a temporary support beam above the opening
- Cut the studs to create the opening, leaving jack studs in place
- Install the header:
- Use doubled 2x lumber with 1/2″ plywood sandwiched between for load-bearing walls (use of engineered lumber or more plys may be required based on the span of an opening, please consult your local regulatory authority before commencing)
- For non-load-bearing walls, a single 2×4 laid flat is usually sufficient
- Install jack studs:
- Cut jack studs to fit snugly under the header
- Nail them to the “king studs” on either side of the opening
- Install the sill:
- For windows, cut a piece of lumber to fit between the jack studs
- Angle it slightly downward to the exterior for drainage
- Add cripple studs:
- Install short studs between the header and top plate
- For windows, add cripple studs between the sill and bottom plate
- Install shims and flashing as needed before fitting the window or door.
Remember to always consult local building codes, as requirements may vary by region.
3. What are the standard framing spacing measurements and why are they important?
Standard framing spacing is typically 16 inches or 24 inches on center (OC), meaning the distance from the center of one framing member to the center of the next. Here’s why these measurements are important:
16-inch OC spacing:
- Most common for wall studs and floor joists
- Provides better support for drywall and exterior sheathing
- Required in areas with high wind or seismic activity
- Allows for easier insulation installation (standard batts are 15″ wide)
24-inch OC spacing:
- Used in some roof framing and in areas with lower structural demands
- Reduces material costs and overall weight of the structure
- May require thicker sheathing or drywall to prevent sagging
Advanced 19 ¼ Spacing:
There is also 19 1/4 spacing as an advanced framing technique, which allows for a reduction of overall building materials by removing 1 stud every 4 feet, and allowing for more insulation in a wall system.
The importance of consistent spacing:
- Structural integrity: Proper spacing ensures even load distribution
- Material efficiency: Standard building materials are designed to fit these spacings
- Code compliance: Most building codes specify required spacing for different applications
- Future modifications: Knowing the spacing makes it easier to locate studs for hanging items or making renovations
When framing, always use a measuring tape and mark your layout clearly. Start your measurements from a consistent point (usually a corner) and account for the width of the framing members themselves.
4. How do I properly install fire blocking in wood frame construction?
Fire blocking is crucial for slowing the spread of fire within concealed spaces in wood frame construction. Here’s how to properly install it:
- Identify areas requiring fire blocking:
- Between vertical and horizontal spaces (e.g., stud cavities and floor/ceiling joist spaces)
- In concealed spaces every 10 feet horizontally
- At interconnections between concealed vertical and horizontal spaces
- At openings around vents, pipes, and ducts
- Choose appropriate materials:
- Solid lumber (at least 2 inches thick)
- Two layers of 1-inch lumber with staggered joints
- 3/4-inch plywood or OSB
- Unfaced fiberglass insulation (at least 16 inches high, securely fastened)
- Installation methods:
- For vertical spaces: Cut blocking to fit snugly between studs and nail in place
- For horizontal spaces: Install blocking perpendicular to joists, nailing through joists into the blocking
- Around openings: Frame around the penetration with fire blocking material
- Seal all gaps:
- Use fire-rated caulk (or spray-foam) to seal any small gaps around the fire blocking
- Ensure a tight fit to prevent air movement
- Specific locations to address:
- Top and bottom of stairways
- Around chimneys and fireplaces
- In dropped ceilings and soffits
Remember, fire blocking requirements can vary by local building codes, so always check with your local building department for specific regulations.
5. What are the key differences between platform framing and balloon framing?
Platform framing and balloon framing are two methods of wood frame construction, each with distinct characteristics:
Platform Framing:
- Most common method in modern construction
- Each floor is framed as a separate unit or “platform”
- Wall studs are typically one story high
- Floor joists rest on top plates of walls below
- Easier and safer to construct, especially for multi-story buildings
- Provides a natural fire stop between floors
- Allows for easier prefabrication of wall sections
- More flexible for future renovations or additions
Balloon Framing:
- Wall studs extend from the sill plate to the roof rafters, often two or more stories high
- Floor joists are supported by a ledger board attached to the studs
- Requires longer lumber, which can be more expensive and harder to find
- Offers better structural stability in some cases
- Lacks inherent fire stopping between floors
- Can be more challenging to insulate properly
- Often requires additional bracing for lateral support
Key Considerations:
- Fire safety: Platform framing naturally creates fire stops at each floor level
- Energy efficiency: Platform framing allows for easier installation of insulation between floors
- Construction ease: Platform framing is generally easier and safer to construct, especially for taller buildings
- Material availability: Balloon framing requires very long studs, which may be hard to source
- Structural performance: Balloon framing can provide better resistance to wind loads in some cases
When working on older homes, it’s important to identify the framing method used, as it affects renovation approaches and safety considerations, particularly regarding fire blocking and insulation.
Bring it to life
Get Started on Your Framing Project Today
Ready to bring your construction vision to life? Contact MHM General Contracting for a comprehensive framing estimate and project plan. Our team is standing by to answer your questions and help you take the first step towards a perfectly framed structure.
Call us at (705) 243-2298 or fill out our online quote request form to get started. Let’s frame your future together in North Bay!